Technical Concept – Aerosols: Principle, Techniques and Application
What are Aerosols? | Principles Of Aerosol
Aerosol spray is a type of gaseous suspension system which creates a gaseous mist of liquid molecules. This dispenser changes the ingredient inside the container into an aerosol where liquid molecules widely and evenly dispersed throughout a gas.
Aerosol is filled in a can which contain propellant and specific solvent under pressure. The mixture is enforced out from container through a small opening present at the top which is under higher pressure, when the container’s valve is opened. As a result of higher pressure inside the can and sudden pressure release, a aerosol mist is formed.
Frequently Asked Questions- Aerosols
It is a substance enclosed under pressure and released as a fine spray by means of a propellant gas.
Aerosols are used in cosmetics such as hairspray, deodorant sprays, foaming agents, sprays and sunscreens etc. In addition, they are used in health care as disinfectants, inhalers, anesthetic preparations, etc. Household preparations in aerosol cans include air fresheners, cleaning agents, car cosmetics, paints and varnishes, etc. They are also very popular in Indistrial application for maintenance related products.
Here are some basic advantages of aerosol spray :
1.Convenient
2.Easy to use
3.Controlled application
4.Compact & portable
5.Long lasting & uniform spray
The goal of aerosol valve is to regulate the entrance/exit of a fluid to or from some source. A specific objective of the aerosol valve is to atomize the contents of the source so that it exits as a fine spray.
There are two types of propellants:
1.A compressed gas (eg. nitrogen or carbon dioxide)
2.A liquid (liquefied gas) (eg. butane,isobutane,propane)
The actuator controls the fineness of the product spray, as well as the amount of product that is dispensed. When you press down on it, the valve is opened. When the valve opens, the pressure is released from the top of the aerosol can and the pressurized propellant tries to escape from the can
Aerosols can be used for for diverse applications like electronic or electrical contact cleaner, dielectric grease coating in aerosol sprays, food grade lubricants in aerosol sprays,zinc rich paint in aerosol sprays popularly known as Galva Coatings, anti-friction coatings, Anti seize in aerosol sprays, moly coating, insulating varnishes to protect electrical & electronic components from unwanted environmental effects,leaks detector sprays to detect unwanted surface defects caused during manufacturing, cleaners etc.
The pressure inside an aerosol is bigger than atmospheric pressure. It ranges from 2 to 8 times the pressure of the atmosphere. This means that the can has to be very strong to withstand the difference in pressure between the inside and the outside.
1.Do not spray or discard aerosol cans on or near a fire. Even if the can is empty, it can still explode or cause injury.
2.Never pierce a hole into aerosols since the can might still be pressurized.
3.Keep aerosols in a safe, cool place away from sunlight. Indirect heat can cause the can to explode.
Road Of Evolution Of Aerosols
1790: Self- Pressurized carbonated beverage introduced in France
1943: Department Of Agriculture researchers Goodhue & Sullivan develop a small aerosol that can be pressurized by a liquefied gas in the USA
1949: The first one-inch aerosol valve is introduced.
1953: Aerosol industry quickly developed in the United States and around the world
Components Of Aerosols
An aerosol canister is actually a complex piece of machinery that helps deliver a steady, concentrated stream of whatever product that is filled inside the tin which is encompassed of following components ;
- Propellant
- Product concentrate
- Aerosol container
- Valve and actuator
Propellants
For the most part, aerosol propellants are responsible for intensifying the pressure in the aerosol container and when the valve is opened it ejects the product from the container and helps in expels the product by atomization of contents or foam production of the product.
Types of Aerosol Propellants
- Liquefied gas propellants
- Compressed gas propellant
When liquefied gas is used as a propellant, under pressure the propellant exists in liquid, and at headspace, it exists as a gas.
When the valve of a container is opened, some of the liquid propellants turn to gas but pressure remains unchanged as time passes. Here, the liquid propellant helps in blending the dissolvable solvent with it completely, for example, LPG, CFC, etc
1. Liquefied Petroleum Gas:
Usually, it is also known as autogas is a blend of Propane, Butane, and n-butane which are natural compounds.
By the blend of these substances as to their distinctive physical-chemical parameters, it is easy to accomplish the required pressure inside the aerosol canister, also making it environmentally safe because these compounds break down in the atmosphere at a quicker rate than the CFCs bringing about a lower ozone-depleting impact.
Features of LPG:
- LPG has fundamentally brought down costs when contrasted with different fuels, for example, Dimethyl ether (DME) and Chlorofluorocarbons, etc.
- It is a steady and pure propellant compound.
- It is an odourless, non-corrosive, and non-toxic gas.
- LPG offers an extensive variety of appropriate vapour pressure and boiling points. The impediment of Hydrocarbon propellants is flammability and explosive.
Chloro Fluro Carbon:
Also known as Freon are completely halogenated paraffin hydrocarbons that contain just carbon (С), chlorine (Cl), and fluorine (F), produced as volatile derivatives of methane, ethane, and propane.
CFCs and HCFCs are colourless, volatile, poisonous fluids and gases with a faintly sweet ethereal odour.
Overexposure at concentrations of 11% or more may cause dazedness, loss of concentration, focal nervous system depression and causes the exhaustion of the ozone layer.
2. Compressed gas propellant:
Compacted gas fuels occupy the headspace over the fluid in the aerosol tin. When the aerosol valve is opened the gas drives the fluid out of the can.
In the headspace, the amount of gas stays constant which on usage pressure decreases because most of the gas escapes the can. For example Carbon dioxide, Nitrous oxide, and Nitrogen.
Carbon dioxide: It has high vapour pressure which is less toxic compared to hydrocarbon propellants. As a result of its low cost, it is mostly used in most aerosol sprays which are normally used in a concentration of 2-4%. While preparation of Carbon dioxide propellant, often Co2 from the air is used by fractional distillation and it does not add extra carbon dioxide to the atmosphere.
Nitrogen: An ideal propellant that helps in keeping up the flow of the most viscous fluid through any container.
It also eliminates oxygen and carbon dioxide from containers completely reducing the possibility of fire catch or acid formation in case of flammable solvents.
Since it is of very high cost and is high pressure with low solvency in numerous solvents, it is normally not used in an aerosol spray.
Because of their low expansion ratio, the sprays are rather wet and the froths are not as steady as created by liquefied gas propellants.
To know more about Propellants click here- Aerosol Propellants
Aerosol Container
Aerosol container more often is a metal can or plastic container, intended to apportion its fluid substance as mist or fog.
The determination of the container for a specific aerosol product depends on its versatility to production techniques, ability to manage the pressure essential for the item and compatibility to solvent and the cost, etc.
Usually, aerosol spray containers are primarily made up of metal, glass, plastics depend on the behavior and characteristic of solvent and propellant used.
Types of Container:
1. Unlined Metal Containers
It is mainly used for solvent based aerosol and used for water based concentrates which contain corrosion inhibitor.
2. Double Lined Metal containers:
This can be used for Water-Based Aerosols where added corrosion protection is required. Interior coatings are made up of – phenolic resin, urethane, or epoxy which are normally applied before container fabrication.
3. Lined Metal containers:
This can be used mainly for a water-based application. Solvents will usually dissolve lining in them. If water-based formulation contains more than 19% of Dimethyl Ether then use Unlined Can with a good corrosion inhibitor package. Dimethyl Ether at this level will penetrate the can lining allowing attack of tin plate. Some of the two-piece containers only come lined, therefore stability must run for the solvent blends.
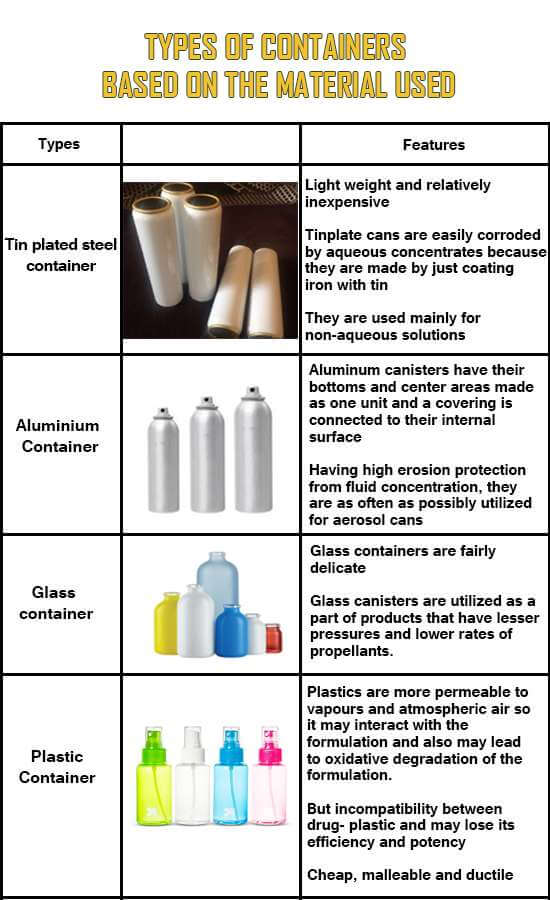
Product Concentrate
The product concentrate is the active drug combined with additional ingredients or co-solvents essential to formulate a steady and effective product. The concentrate can be a solution, suspension, emulsion, semisolid, or powder.
For aerosols, it is important to completely study the kind of concentrate or formulation, choice of the propellant gas, concentrate/gas proportion, and managing the gas pressure in agreement with the discharged state, method for utilizing and utility of their contents.
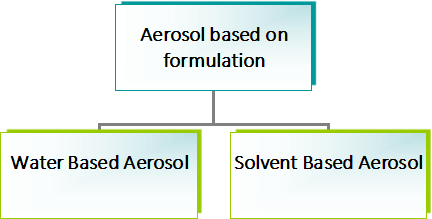
Water-Based (Emulsions, Dispersions): Water-based products are normally contained inlined and double lined cans (phenolic resin, urethane, or epoxy linings).
They are also contained in unlined cans if an effective corrosion inhibitor is used. – Propellants normally used in aqueous products are Hydrocarbon, Hydrocarbon Blends, Dimethyl Ether, Hydrofluorocarbons, and Nitrogen. The only propellant that is not normally used in aqueous formulas is Carbon Dioxide. This propellant in an aqueous medium will form carbonic acid causing potential corrosion problems and can also affect the physical parameters of the finished aerosol product.
Because of cost, the majority of water-based aerosols are most likely dispensed using a hydrocarbon propellant at a 4 to 10% level.
Since Dimethyl Ether is soluble in water if over 19% DME is required to dispense the contents, a good corrosion inhibitor must be used because DME will penetrate can linings allowing attack of the tinplate. Nitrogen is less commonly used. – Corrosion Inhibitors, anti-oxidants, and biocides are typically used in aqueous formulas.
Solvent Based (Water in Oil, Dispersions): Unlined containers are normally used because most solvents will dissolve the interior coating of the can.
If you have a moisture content of greater than 0.1% present in the concentrate, a corrosion inhibitor will most likely be necessary. In certain situations, even moisture content of less than 0.1% could cause interior can corrosion.
Propellants used in solvent formulas are Hydrocarbons, Hydrocarbon blends, Hydrofluorocarbons.
Solvent Formulas will normally require a higher level of the liquified gas propellant. Propellant levels as high as 1/3 of the Net Content of the product may be necessary to completely discharge the can. It is normal for the DME, Hydrofluorocarbon, and Hydrocarbon propellants to act as solvents in these formulas.
Carbon Dioxide levels in solvent formulas will run between 2 to 7% and Nitrogen will run about 0.5 to 2%.
The saturation level of Carbon Dioxide in the concentrate is greater than that of Nitrogen.
Valve and Actuator
The special characteristics of aerosol products are largely ensured by the concentrate and the propellant gas but the state in which the product is discharged often varies depending on the type of valve, actuator (used when the product is sprayed out as a mist), and spout (used when the product is discharged other than in mist form) mechanisms used.
Components of Valve:
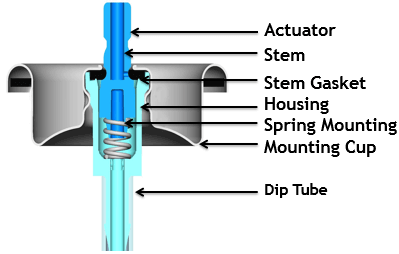
- Actuator: Controls pattern & flow
- Stem: Controls flow
- Stem Gasket: The “ON/OFF” Switch
- Spring: Closes Valve
- Housing (Body) : Encloses spring/stem & controls flow
- Dip Tube: Draws product up & valve
- Mounting Cup (With mounting & gasket): The link between the can & valve
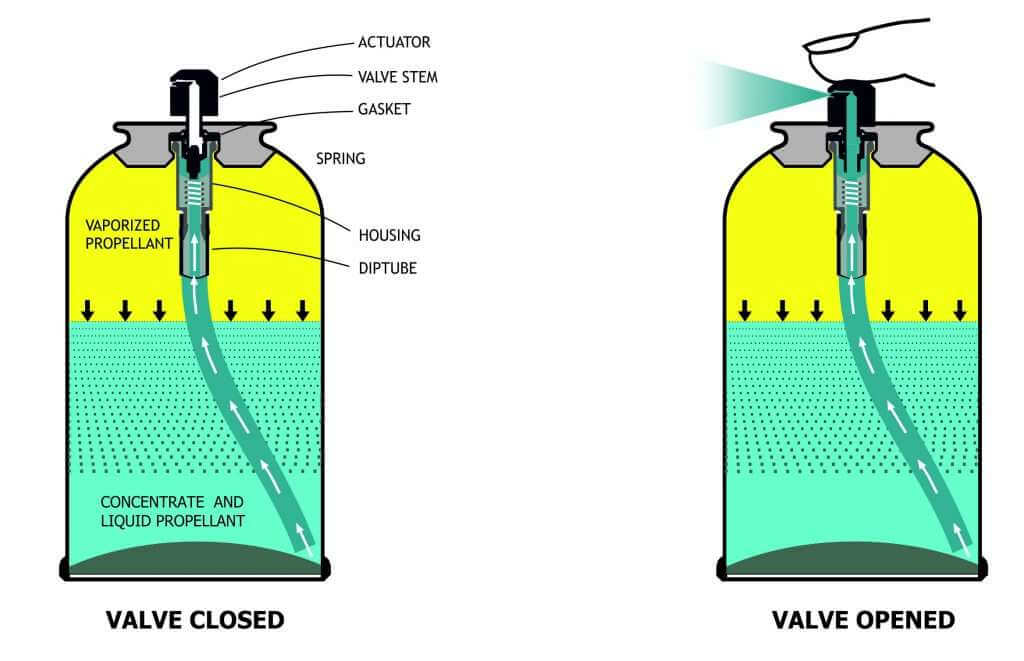
Operating Principle Of Valve
Pressure on the actuator depresses the stem. This movement interrupts the sealing action of the gasket and exposes the stem orifice to the pressurized flow of the product in the container, thereby opening the valve. When the actuator is released, the spring returns the stem orifice to the sealed position, closing the valve.
Actuators: Actuators and spouts form the outlets through which the aerosol contents are discharged.
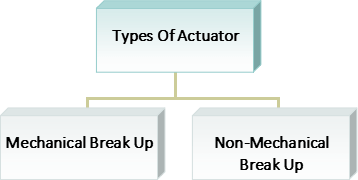
- Mechanical Break Up: Incorporates a swirl chamber results indiscernible pattern & shape.
- Non-Mechanical Break Up: Direct flow through the actuator usually results in a stream.
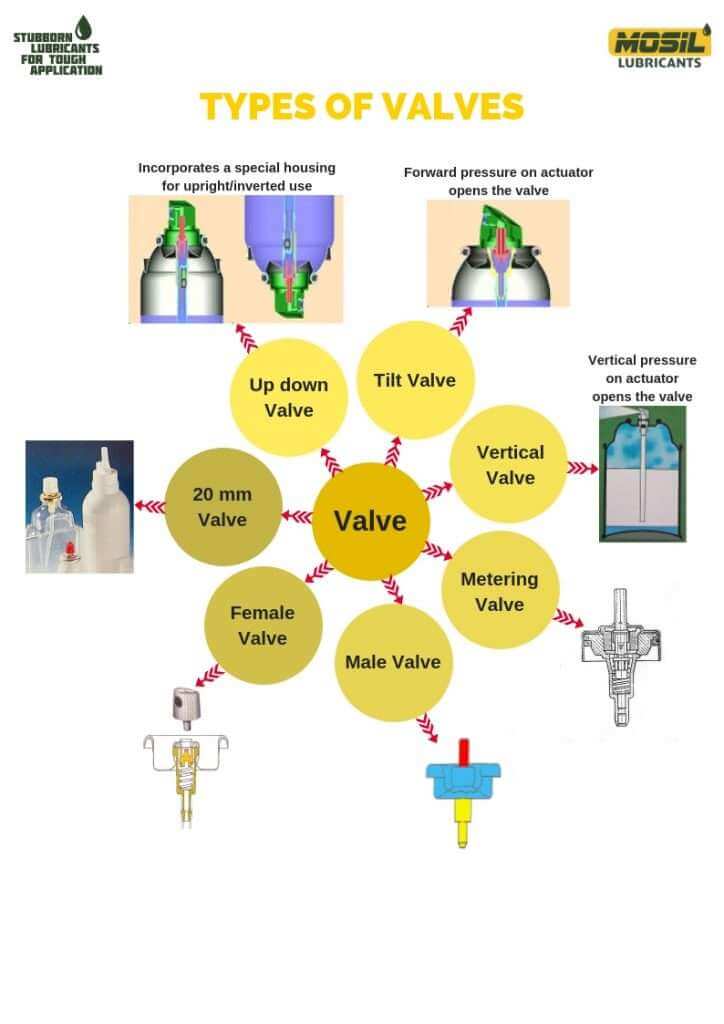
Characteristics Of Aerosols
- The pressure of the propellant discharges the contents. If the contents are a solubilized system containing 40-70% liquefied gas, they are sprayed out as a mist, but if they are an emulsion system containing 5-15% liquefied gas, the contents are discharged as a foam.
- The extension tube which is attached to the actuator makes the product flow easier and helps in reaching difficult crevices.
- The bottom part of the container is not flat which helps in controlling increased pressure inside the canister.
- To empty out the liquid inside the can completely, the dip tube is aligned with the colour marking on the valve plate.
Advantages & Disadvantages Of Aerosols
Advantages-
- Portable
- Long-Lasting
- Particle size/pattern control
- Continuous spray
- Convenient
- Easy to Use/Immediate Use
- Controlled Application
- Compact
Disadvantages-
- Chlorofluorocarbon fuels cause Ozone layer exhaustion
- Inflammability
- Toxicity
- Explosive
- Costly
Applications Of Aerosols
- Automobile ( Starter Motors, Drive Chains, Car locks, Spark plugs, Door Hinges, Push back and tilting systems)
- Industrial (Overhauling machinery, crane hook bearings, and wheels, Lubricates and opens jammed bearings, Loosens jammed nuts and bolts, Power tools, Jigs & fixtures).
- Ordnance ( Guns, Precision fitting, Linkages )
- Electrical Equipment (Alternators, Motors, Relays, Circuit Breakers, Fuses, Potentiometer Relays, Switch gears, etc.)
- Pneumatic Systems (Sticky solenoid valves, Clogged needle valves, Automatic valves & cylinders)
- Household (Drawers, Hinges, Pins, Sliding Contact at Windows, Sewing Machines, etc.)
- Domestic (Mixers and Grinders, Hand Tools, Washing Machines, Collapsible Grills, Folding Chairs and Tables, TV, Radio, and Tape recorder tuners, etc.)
- General Purpose (Sliding Windows and door channels, Locks, Switches, Bicycle chains and sprockets, rolling shutters, elevator doors, etc.)
Steps Towards The New Frontiers Of Aerosols
Due to their convenience, the use of aerosol cosmetics has been increasing in recent years. The following describes special types of aerosol container which have been developed;
- Special aerosol containers: Special aerosol containers comprise different types of the compartment can using either an inner bag or piston system.
- Inner bag system: This type of compartment can have a soft inner bag (made from PE or soft aluminum) which is filled with the aerosol contents while the outer part of the container is filled with gas. The pressure of the gas squeezes the inner bag causing the aerosol contents to be discharged.
- Piston system: In this type, there is a piston inside the container. The part of the container above the piston is filled with the aerosol contents and that below it with gas, the pressure of which pushes up the piston valve discharging the contents from the container.
Conclusion
When designing aerosol products, it is necessary to consider such environmental aspects as effect on the ozone layer, atmospheric pollution, and global warming.
With this in mind, positive efforts are now being made to reduce the amount of gas used and develop containers that use no gas at all. As examples of the latter, research is now being done on manual atomizers, electric sprayers, compressed air, and other systems for mist-form products and, in the case of liquid-form products, dispensers, and systems that discharge the concentrate as a foam. Some of these systems are already being applied in commercial products.
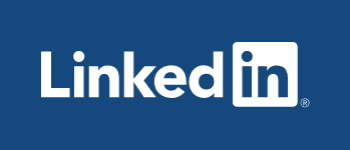