Lubrication linked with a maintenance strategy
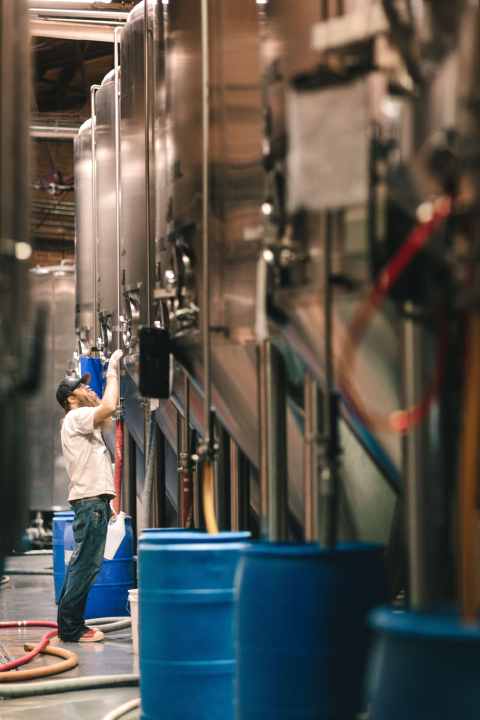
Regular Maintenance is frequently considered as an evil necessity and often delayed or cancelled to meet production demands. Taking equipment out of service to improve functionality can be a tough call, especially if the only maintenance activity is lubrication. As the industry has evolved, so have the practices and philosophies for how and when to perform maintenance and lubrication.
More options and tools are now available to guide the actions of personnel for nearly all lubrication tasks. However, to truly understand how this evolution has changed the landscape, you must know where maintenance began and where it is today.
Industrial Maintenance Beliefs
Maintenance is required if the machine fails to satisfy the minimum level of specification performance and is optional if the partially failed machine still satisfies the minimum level of specification performance.
Industrial Maintenance broadly takes place in four phases.
- Failure Detection
- Fault isolation and measures to act over.
- Corrective action on faults.
- Operational verification
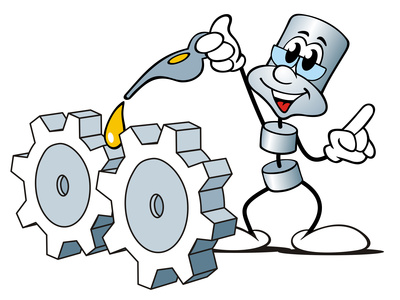
Lubrication activities
In a lubrication program, there are tasks for applying lubricants, analyzing their state, and eventually disposing of them once they reach the end. Beyond these front-line tasks are management activities to ensure work is completed properly. Perhaps the simplest lubrication task involves the use of a grease gun. However, these devices have been improved in recent years and now incorporate advanced technology. Before utilizing a grease gun, be sure to consider the task in relation to the different maintenance philosophies discussed previously.
This same methodology applies to oil applications. While you may rely on the rotating motion of a machine to apply oil to various internal components, you control many other factors that can provide an indication of success. The workload will vary greatly depending on the mindset of the individual or organization.
Lubricant analysis strategies
Lubricant analysis falls into the realm of condition monitoring but can be used in various ways to determine what is happening inside a mechanical system. It also can be divided into four different strategies:
- Reactive – An oil or grease sample is taken only after a potential problem is identified via a sensory inspection.
- Preventive – Routine samples are extracted, but the results are not analyzed.
- Predictive – Good samples are obtained and analyzed, with the action taken on results from the lab.
- Proactive – New lubricants are sampled prior to service. Samples are taken from the right place, in the right way, using the right tests and with the right interpretation strategy.
Philosophy
Most people are familiar with the term “reactive maintenance.” This approach involves repairing machines only after a breakdown or failure. Too often, reactive philosophies are adopted by organizations that are short on the manpower or stuck in the “that’s how we’ve always done it” mentality. This leads to overblown maintenance budgets, poor operational performance, and a staff that is constantly firefighting. As someone who worked in a reactive mode for years, I can attest to the stress it puts on your team. For instance, it was difficult to know when you were going home each day, if at all. Even on weekends or holidays, there was always the risk of being called into work. This maintenance philosophy is not sustainable and has largely been relegated to non-critical or small pieces of equipment.
In an effort to move away from the reactive state and in cases where safety is paramount, planned or scheduled maintenance was implemented. Known as preventive maintenance, this approach entails having a set period or interval when maintenance is scheduled and then performed. The airline industry provides a good example of this philosophy. Running an airplane engine until failure is not an option because of the safety ramifications. Therefore, maintenance is scheduled based on the number of hours or flights. The same practice was adopted in the industry. This included closely following OEM recommendations or intervals to prevent a failure. You probably use a similar method with your vehicle’s maintenance. By introducing a scheduling component to your maintenance activities, you can add some direction and continuity to a daily process.
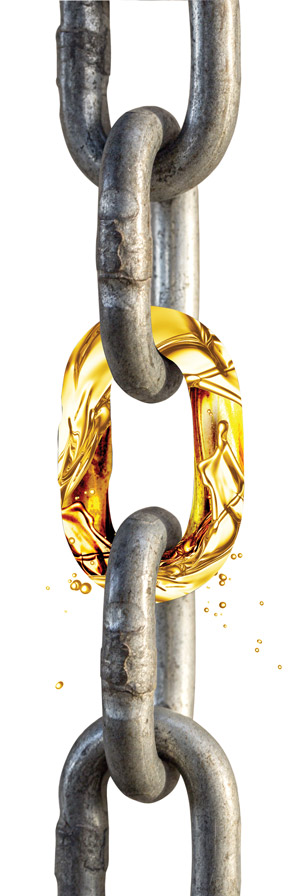
Although preventive maintenance can help reduce the chaos of failures, it can still result in high maintenance costs when good parts are replaced.
More recently, new tools and accessories have become available to aid in equipment monitoring and catching potential issues earlier. This monitoring of failure symptoms and faults is known as predictive maintenance. The most common forms of this approach include using vibration analysis, ultrasound, thermography, oil analysis, and a host of other technologies to provide an early warning of an impending problem.
Predictive maintenance works well for machines that run continuously and often results in a reduction of unplanned downtime. However, it usually comes with considerable upfront costs, not just for the necessary tools but also in training the individuals who are expected to capture the pertinent data. Diligence is required to ensure data is collected from the same place and in the same manner each time. Inconsistent practices will skew the data and make it much more difficult to take appropriate action.
Rather than fixing machines, proactive maintenance eliminates what causes them to fail. It can be used to extend equipment life, as opposed to simply improving the process for repairs or identifying when a machine is going to fail. Proactive maintenance focuses on the root causes of failure and addresses them before they lead to an eventual problem. Much of proactive maintenance occurs before a machine is ever turned on, including alignment and balancing. Without a proactive mindset, equipment failures will continue to plague most maintenance departments. Analyzing what went wrong and taking steps to prevent it from happening again are the hallmarks of being proactive.
Inference - Never ignore inspections
Inspections are often ignored as the foundation of a world-class lubrication program. Personnel who walk by machines every day are the greatest source of information to drive your program forward.
Greater emphasis must be placed on the inspections, Just having a checklist or making simple rounds is not enough. Digging deeper into what you notice about the machine will be an extremely valuable activity that will bear fruit in all aspects of maintenance, regardless of the philosophy employed.
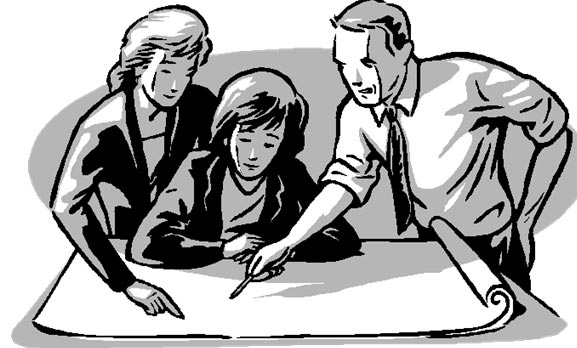
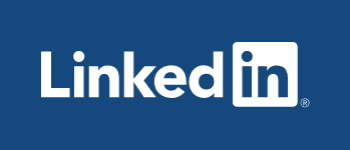